Gravure Laser Cylinders
Rotogravure Printing Cylinder
Introducing a specialized laser-friendly cylinder designed to seamlessly integrate with the latest technology in digital gravure. In digital gravure, computer-directed lasers are employed to meticulously carve cells of varying depths and sizes into the surface of cylinders.
-
Digital laser engraving for rotogravure.
- Perfect for use with rotogravure printing cylinder.
- Initially, a rotary gravure steel cylinder is subjected to electroplating, resulting in the creation of a uniform and smooth surface layer made of copper or zinc. To minimize heat conduction and the convection of molten materials during the gravure process, galvanic plating is introduced to the zinc/chrome layers, aligning them with the required surface structure and durability standards.
- The representation of image information occurs through the engraving of microscopically small cell volumes into the copper or zinc surface. These cells facilitate the transfer of printing ink onto the substrate.
- To ensure a prolonged lifespan, particularly under demanding abrasive conditions within the printing press, a thin chromium layer is applied. The use of a doctor’s blade ensures that only the quantity of ink designated by the cell size is transferred.
- Following print runs, immediate cleaning of the cylinder is essential to preserve the integrity of the image surface.
-
Туре: Seamless Laser Gravure Sleeve
Base material: Nickel, copper
Plating material: Engravable copper, then chrome
Surface hardness: HV500/600/900
Sleeve wall thickness: 76 microns to 558 microns
Diameter: 80-600mm
Length: 100-5000mm
Engraving by: Digital Laser
LPI: 25~300
Washout: Solvent-based/Water-based
-
Precision: Direct laser micro-structuring offers the benefit of remarkable precision, with a beam-pointing accuracy of approximately 1 micron. This precision results in higher machining rates, precise focusing with high resolution and the added advantage of digital flexibility that conventional engraving methods cannot match.
• Uniformity: Laser technology operates as a non-contact tool, ensuring uniformity across the entire imaging surface of the cylinder. This predictability and repeatability represent a significant advantage over electromechanical gravure, which employs a diamond stylus.
• Ink transfer: Laser-engraved cylinders provide exceptional control over cell geometry and surface texture, allowing for the creation of entirely new cell configurations that optimize ink transfer characteristics and printability for specific colour percentages and tone values on various print substrates. This is critical for achieving consistent, pinhole-free ink transfer, resulting in enhanced print gloss and reduced print mottle, particularly when using higher-viscosity inks. Compared to traditional electro-mechanical engraving, laser engraving can reduce ink consumption by up to 30%.
• Variability: Laser engraving allows for greater variability in cell size and shape while maintaining a high print density. The dynamic control of the laser beam diameter enables individual modifications to cell width and depth before printing. Such variable cell shapes are unattainable with electromechanical engraving.
• Time: Thanks to the high repetition rate of the laser beam, digital laser engraving is approximately 17 times faster than electromechanical gravure processes. Laser-engraved cylinders also minimize the impact of press printing speed on print quality while preserving stable tone values.
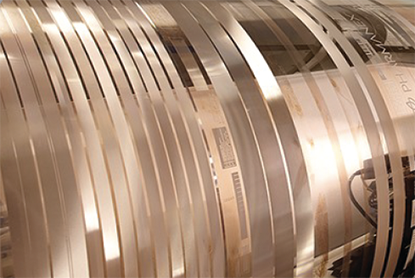
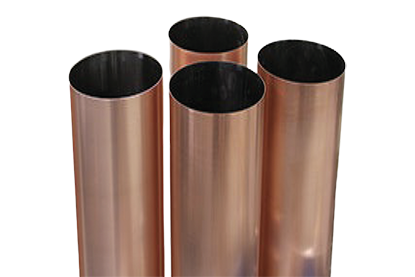
Business Hours
Monday - Friday: 8:00am - 17:00pm