Gravure Sleeve Cylinders
Sleeve Gravure Printing Cylinder
A gravure printing sleeve mandrel is the engraved image carrier utilized in gravure printing and generally consists of a steel cylinder base or a foundational metal structure that supports the engraved image-bearing layer.
- The gravure printing cylinder is used in publication printing for magazines, newspapers, add inserts, catalogues.
- Other substrates such as gift wrapping, wallpaper, postage stamps, thin film, nylon, etc.
- Packaging printing, including polyethylene, polypropylene, polyester, laminates for furniture, vinyl, BOPP.
- Steel gravure cylinder bases undergo an initial plating process, where they are lightly coated with either copper in a cyanide bath or with nickel.
- Following this, each cylinder is transferred to an acid copper sulfate bath and allowed to grow to the desired size.
- The meticulous management of the production process for a high-quality cylinder ensures an exceptionally precise engraving surface, promoting optimal image quality and preserving cell wall integrity.
- After the engraving process is finished, the engraver applies a chrome layer, and polishing stones are employed to rectify any inaccuracies in the plating.
Base material: Steel welding pipe/seamless steel tube
Plating material: Engravable copper, then chrome
Surface hardness: ›HRC50
Roughness: ≤Ra 0.16
Diameter: 100-400mm
Length: 320-1800mm (normally 50mm longer than rubber roller)
Engraving by: Electro-mechanical, laser, or chemical etching.
Thermal deformation: ≤0.01mm
Concentricity: 0-15 microns
Straightness: ≤0.2mm
- Variability: Variable wall thickness offers greater diameter variability compared to thin-film technology.
- Durability: These cylinders are easily electroplated, enabling them to withstand increased printing pressure and high-volume print runs without experiencing cell wall breakdowns.
- Quality: The copper image-carrying layer ensures the highest degree of structural and functional integrity, resulting in consistently high print quality.
- Consistency: Color laydown and image rendering quality remain consistently stable.
- Versatility: Continuous image data enables seamless print runs and accommodates a wide range of porous or non-porous flexible substrates.
- Ink Laydown: The depth and size of engraved cells allow for greater ink laydown compared to other processes.
- The use of different shafts at various stages of production, such as engraving, plating, and printing, can introduce inaccuracies into both the engraved and printed images.
- Since gravure printing necessitates one cylinder for each colour, it becomes costly for short print runs.
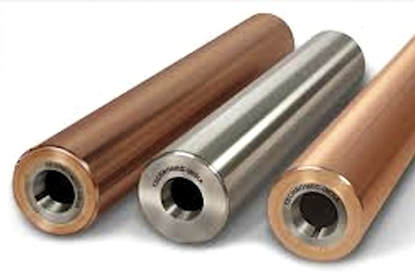
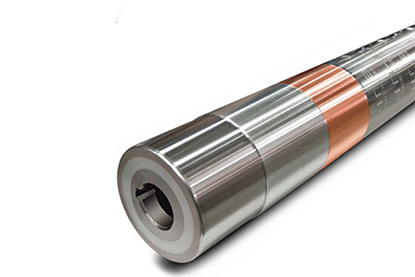
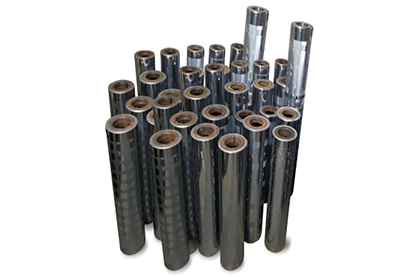
Business Hours
Monday - Friday: 8:00am - 17:00pm
© 2024 Packadvance Innovative Technology | Privacy Policy | Website design by TSD Group