Gravure Shaft Cylinders
Shaft Cylinder
A gravure shaft cylinder is ideally suited for long-run print lines. As the preferred engraved image carrier, it offers an impressive density range and the added advantage of sustaining precise print quality over time.
- Publication printing for magazines, newspapers, and catalogues.
- Packaging printing, including cardboard, plastic film, aluminium foil, laminates and vinyl where printing on a variety of substrates is needed.
- Gift wrapping, wallpaper, postage stamps, and the text on candies and tablets, etc.
- A gravure printing cylinder typically comprises an underlying steel base, to which an electroplated layer of copper is added utilizing a sulfuric-acid electrolyte.
- On top of the copper, a pre-polymer layer covering the metallic surface is added, that can be imaged by either electro-mechanical (diamond cutting) or digital laser etching.
- After engraving, the etched copper surface is plated with a thin layer of chrome to protect it from abrasion from the doctor’s blade during printing. This chrome surface is polished before printing.
- Finally, the Total Indicated Run-out (TIR) of the cylinder is measured to ensure that a cross-section of the cylinder must be as close to a perfect circle to avoid generating any “bumps” or printing distortions.
Type: Seamless shaft cylinder
Material: Steel
Surface Hardness: HV500/600/900
Diameter: 80-600mm
Length: 100-5000mm
Engraving by: Electro-mechanical, laser, or chemical etching.
LPI: 25~300
TIR: <0.03MM
Washout: Solvent-based/Water-based
-
Long-lasting: Gravure steel cylinders are initially coated with copper for engraving and then finished with chrome, resulting in exceptional durability. It’s common to achieve print runs of 2 million to 3 million from a single cylinder set. Once the cylinder is no longer needed, the chrome and copper can be removed, and the steel base can be reused.
-
Quality: Gravure printing boasts fewer variables, ensuring a more consistent print quality.
-
Consistency: This is a hallmark of Gravure due to its direct printing process, which maintains stable colour laydown and image rendering quality.
• Versatility: Gravure allows for continuous image data, facilitating seamless print runs and accommodating a wide range of porous or non-porous flexible substrates.
• Ink: The depth and size of engraved cells permit a higher ink laydown compared to other processes.
• Productivity: Gravure presses operate at high production speeds, capable of averaging up to 1000 meters of printing per minute.
- Due to its initial high cost and time needed to engrave gravure cylinders, gravure printing is not appropriate for short runs and is better suited to very long runs of up to and beyond a million impressions.
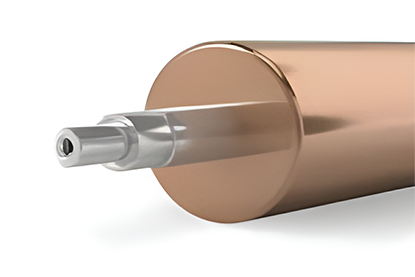
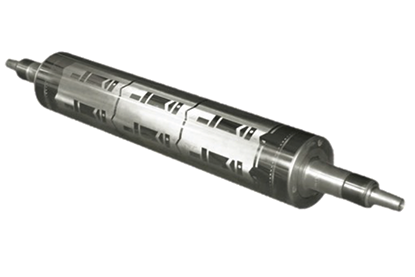
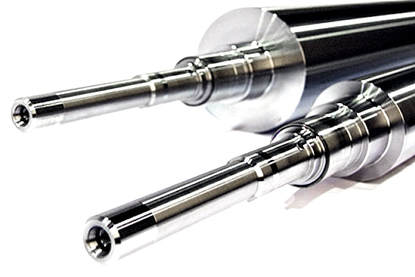
Business Hours
Monday - Friday: 8:00am - 17:00pm